Die Aushärtungsmechanismen der Klebstoffe
Loctite Worldwide Design Handbook
- anaerob aushärtende Klebstoffe
- durch UV-Licht aushärtende Klebstoffe (auch mit sekundären Aushärtesystemen)
- anionisch aushärtende Klebstoffe (Cyanacrylate)
- mit Aktivatoren aushärtende Klebstoffe (modifizierte Acrylate)
- durch Feuchtigkeit aushärtende Klebstoffe (Silikone, Urethane)
- warmhärtende Klebstoffe (Epoxidharze)
Anaerob aushärtende Klebstoffe
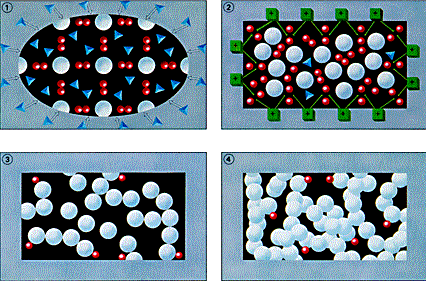
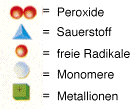
- gute Temperaturbeständigkeit (von –55° C bis max. +230° C)
- schnelle Aushärtung
- einfache Dosierbarkeit mit automatischen Dosiergeräten, da nur eine Komponente
- Feinstbearbeitung von Werkstücken nicht erforderlich; Rautiefen zwischen 8 und 40 µm sind zulässig
- gleichzeitige Dichtungswirkung mit ausgezeichneter chemischer Beständigkeit
- gute Beständigkeit gegenüber mechanischen Schwingungen
- gute Beständigkeit bei dynamischen Dauerlasten
Passive und aktive Werkstoffe und ihre Auswirkung auf die anaerobe Aushärtung
Schnelle Aushärtung
Bronze
Kupfer
Eisen
Stahl
Langsamere Aushärtung*
Aluminium (mit niedrigem Kupfergehalt)
Keramik
Chromatschichten
Glas
hochlegierter Stahl
Nickel
Oxidschichten
Kunststoffe
Silber
rostfreier Stahl
Zinn
Zink
* Aktivatoren für schnelle Fixierung verwenden
- Fügeteile (Abb. 4)
- Spalt zwischen den Werkstücken (Abb. 5)
- die Temperatur (Abb. 6)
- den Aktivator (Abb. 7)
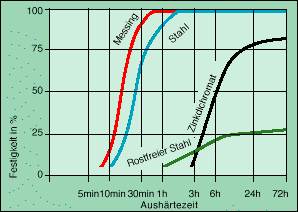
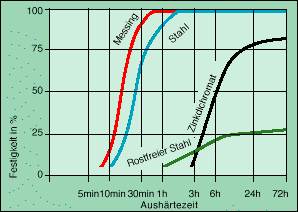
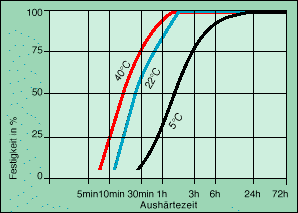
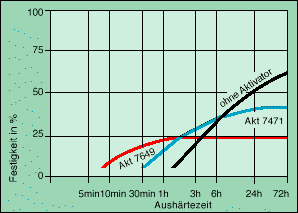
Durch UV-Licht aushärtende Klebstoffe
- Tiefenaushärtung durch UV-Strahlung
- Oberflächenaushärtung durch UV-Strahlung
- Aushärtung durch Sekundärsysteme
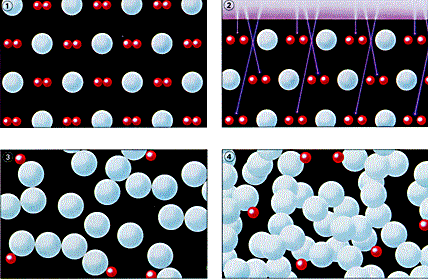
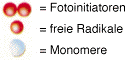

Tiefenaushärtung
UV-Systeme, die ein sehr strahlungsstarkes Licht mit Wellenlängen von 300 bis 400 nm (langwelliges UVA-Licht) ausstrahlen, sind besser geeignet, wenn man eine größere Aushärtungstiefe erzielen möchte (siehe Abbildung 10).
Oberflächenaushärtung
Beim Vergießen und Beschichten mit UV-aushärtenden Produkten ist die Oberflächenaushärtung von großer Bedeutung. Werden ungeeignete UV-Lampensysteme eingesetzt, kann eine klebrige Oberfläche zurückbleiben. Um dies zu verhindern, muss die UV-Strahlungsquelle eine hohe Intensität im Wellenlängenbereich unterhalb von 300 nm erzeugen.
Dadurch kann die unerwünschte Reaktion der Klebstoffoberfläche mit dem Luftsauerstoff, die das Aushärten des Produktes an der Oberfläche verhindert, weitgehend unterbunden werden (siehe Abbildung 11). Die Strahlungsspektren der „energiereichen“ Loctite-UV-Lichtsysteme garantieren eine zuverlässige Aushärtung, ohne dass eine klebrige Oberfläche zurückbleibt.
Aushärtung durch Sekundärsysteme
Falls die UV-Strahlung nicht zu allen mit Kleber benetzten Stellen gelangt, hat Loctite Klebstoffe entwickelt, die über ein zweites Aushärtesystem verfügen. An den Schattenstellen kann eine vollständige Polymerisation durch folgende Sekundärsysteme erreicht werden:
- Anaerobe Aushärtung
- Aushärtung durch Wärme
- Aushärtung mit Aktivatoren
- Aushärtung durch Luftfeuchtigkeit
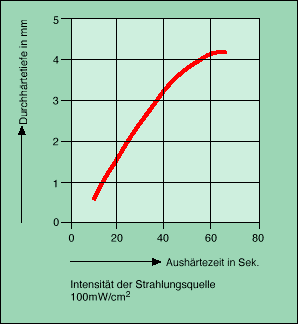
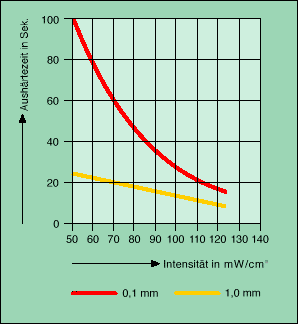
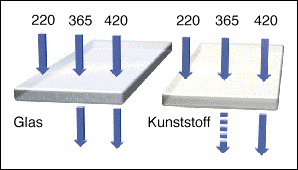
- hohe Festigkeit
- großes Spaltfüllvermögen
- sehr kurze Aushärtezeiten für das Erreichen der Handfestigkeit
- gute bis sehr gute Medienbeständigkeit
- gute Dosierbarkeit mit automatischen Dosiersystemen, weil es nur eine Komponente gibt
Anionisch aushärtende Klebstoffe (Cyanacrylate)
- Kleben von Glas und Glas oder von Glas und Metall
- Kleben transparenter Kunststoffe
- Abdichten elektronischer Bauteile (z. B. Relais)
- Kleben von elektronischen Bauteilen auf Leiterplatten
- Beschichten von Leiterplatten (Elektronik)
- Abdichten/Kleben bei Hochtemperaturanwendungen
- Fügen von Metallteilen (Welle-Nabe-Verbindungen) und Aushärtung überschüssigen Klebstoffes durch UV-Licht zur raschen Fixierung
- Kleben von Metall- und Kunststoffteilen und Aushärtung überschüssigen Klebstoffes durch UV-Licht zur raschen Fixierung

Aushärteverhalten von Cyanacrylatklebstoffen in Abhängigkeit von der relativen Luftfeuchtigkeit.
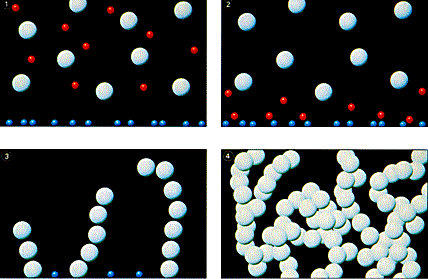
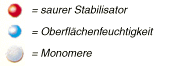
Cyanacrylatklebstoffe sollten einseitig und sparsam aufgetragen werden. Die beste Klebung wird erzielt, wenn nur so viel Klebstoff aufgetragen wird, wie zum Ausfüllen des Fügespalts erforderlich ist.
Wie bereits erläutert, hängt die Aushärtegeschwindigkeit von der Feuchtigkeit auf der Klebefläche ab. Um die Aushärtung zu beschleunigen oder um von der Luftfeuchtigkeit unabhängig zu sein, können Aktivatoren eingesetzt werden. Auch überschüssiger Klebstoff oder ein offener Klebstofftropfen (z. B. für das Kleben von Drähten) härtet bei Verwendung von Aktivatoren innerhalb von Sekunden aus.
- sehr hohe Scher- und Zugfestigkeiten
- sehr schnelle Aushärtung (Fixierung innerhalb Sekunden)
- kleben fast alle Werkstoffe
- gute Alterungsbeständigkeit
- poröse Werkstoffe und leicht saure Oberflächen
- schwer zu klebende Kunststoffe, sehr schnelle Fixierung
- höhere Viskosität mit gutem Spaltfüllvermögen
- poröse Werkstoffe, mit hervorragendem Spaltfüllvermögen, gelartige Viskosität
- geringe Ausgasung, schwacher Geruch, wird eingesetzt, wenn optische Eigenschaften Priorität besitzen
- Kleben ungleicher Werkstoffe, flexibles Cyanacrylat, wird häufig für das Kleben von Metall und Kunststoff eingesetzt
- Kleben von Metall und Metall oder Metall und anderen Werkstoffen
- Kleben unterschiedlicher Werkstoffe, beste Temperatur- und Wärmealterungsbeständigkeit
Mit Aktivatoren aushärtende Klebstoffe (modifizierte Acrylate)
Um auf flüssige Aktivatoren verzichten zu können, stehen auch Acrylat-Klebstoffe zur Verfügung, bei denen der Aktivator dieselbe Konsistenz wie der Klebstoff aufweist. Hierbei handelt es sich um Zweikomponentensysteme, bei denen Klebstoff und Aktivator getrennt aufgetragen werden, und zwar Raupe neben Raupe oder Raupe auf Raupe. Wenn die beiden zu klebenden Teile zusammengefügt werden, vermischen sich die Klebstoffkomponenten durch den Fügeprozess. Besitzt der gemischte Klebstoff eine Topfzeit von 5 Minuten oder mehr, kann auch ein statischer Mischer verwendet werden. Dies bietet den Vorteil, dass bereits vorgemischter Klebstoff dosiert wird und die Durchmischung nicht vom Fügeprozess der Teile abhängt.
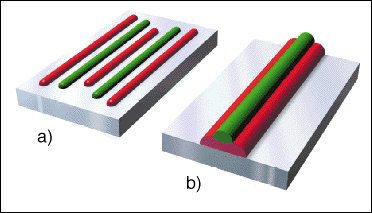
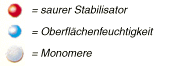
- sehr hohe Scher- und Zugfestigkeiten
- gute Stoßfestigkeit
- großer Einsatztemperaturbereich (–55° C bis +120° C)
- kleben fast alle Werkstoffe
- großes Spaltfüllvermögen (insbesondere vorgemischte Acrylate)
- gute Medienbeständigkeit
- Kleben von Lautsprechern
- Magnetkleben
- Strukturelles Kleben
Durch Luftfeuchtigkeit aushärtende Klebstoffe
Zu dieser Gruppe gehören zwei allgemeine chemische Substanzen:
Silikone:
Diese Werkstoffe vulkanisieren bei Raumtemperatur durch Reaktion mit der Luftfeuchtigkeit (Raumtemperaturvulkanisierung = RTV). Im Vergleich zur anionischen Reaktion der Cyanacrylate, bei der die Feuchtigkeit den Stabilisator neutralisiert, nutzen Silikone das Wassermolekül zur Vernetzung. Das heißt, dass die Feuchtigkeit in das Silikon an die Stelle eindringen muss, an der die Vulkanisierung stattfindet. Wird das Wassermolekül in die Bindung zwischen den Silikonmolekülen integriert, wird ein Nebenprodukt freigesetzt. In Abhängigkeit der Aushärtungschemie kann das freigesetzte Nebenprodukt sauer (z. B. Essigsäure), basisch (z. B. Amin) oder neutral (z. B. Oxim oder Alkohol) sein.
Die Aushärtegeschwindigkeit dieser Klebstoffe hängt vorrangig von der relativen Luftfeuchtigkeit ab.
Die Eigenart des Aushärtemechanismus führt dazu, dass Silikone vom äußeren zum inneren Bereich der Klebung vulkanisieren. Aufgrund der erforderlichen Feuchtigkeitsmigration zum Ort der Vernetzung ist die Aushärtetiefe auf 10 – 15 mm begrenzt.
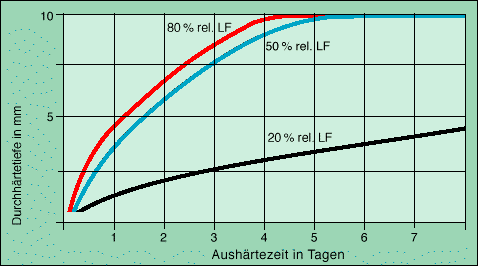
- außerordentliche Wärmebeständigkeit (mehr als 230° C)
- elastisch, zäh, hohe Dehnung
- niedriger bis mittlerer E-Modul
- wirksame Dichtung gegen zahlreiche flüssige Medien
- ausgezeichnetes Spaltfüllvermögen
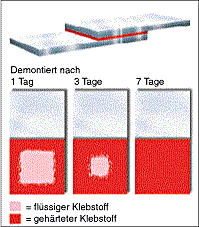
- Flächendichten und Abdichten in der Automobilindustrie
- Abdichten bei Hochtemperaturanwendungen
- Abdichten und Kleben (insbesondere bei kleinen Werkstücken)
- UV-Licht-Aushärtung
- Abdichten und Vergießen (neutrales Nebenprodukt)
- Beschichtung von Leiterplatten
- UV-Licht-Aushärtung
Polyurethane:
- ausgezeichnete Zähigkeit
- Elastizität, hohe Dehnung
- ausgezeichnetes Spaltfüllvermögen
- nach der Aushärtung überlackierbar
- ausgezeichnete chemische Beständigkeit
Warmhärtende Klebstoffe
Die Aushärtezeit hängt mit der Aushärtetemperatur zusammen – je höher die Aushärtetemperatur, umso kürzer ist die Aushärtezeit. Normalerweise ist eine Mindesttemperatur zur Aktivierung des Härters und zur Initiierung der Polymerisation erforderlich.
- Kleben
- Abdichten
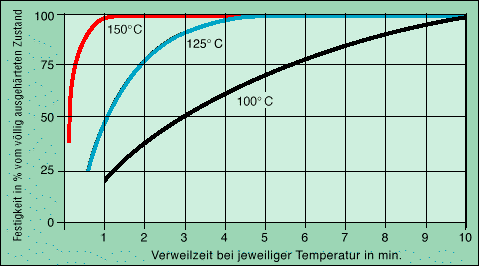
Die warmhärtenden Klebstoffe decken eine große Bandbreite an Eigenschaften ab und sind stark von der chemischen Basis (z. B. Epoxid, Methacrylat) abhängig.
- mittlere bis hohe Festigkeit
- gute Adhäsion zu vielen Werkstoffen
- gutes Spaltfüllvermögen
- gute bis sehr gute Beständigkeit gegenüber Medien
- Chipkleben (Elektronik)
- Relaisabdichtung
- Imprägnieren
- Schraubensichern, Gewindedichten, Flächendichten, Fügen von Welle-Nabe-Verbindungen
- Kleben
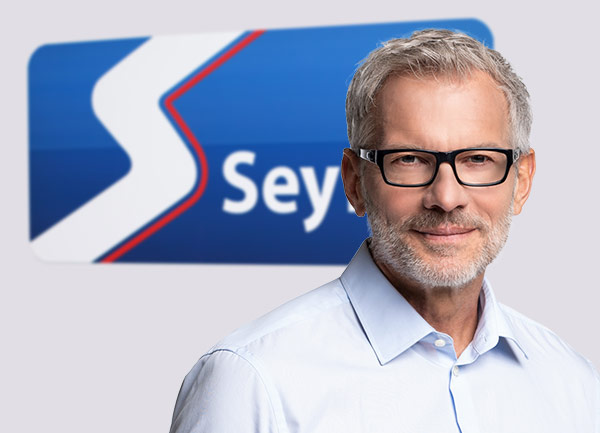